Launch of innovative vision-based tactile robot hand
- FingerVision
- Jun 27, 2024
- 2 min read
FingerVision recently launched a new lineup of robot hands for various industries including automobiles, electrical equipment, materials, semiconductors, logistics, and medical care. In addition to the vision-based tactile robot hand that was sold as standard with one size and shape, and two types of tactile information (force and slip), in order to meet various needs, we have developed a product lineup with a wide variety of robot hand tips (hereinafter referred to as fingers) and additional visual and tactile information (not only force and slip, but also firmness and positional information).
FingerVision's vision-based tactile robot hand can now be used not only for the food industry, where on-site implementation of robot systems is already ongoing, but also for a variety of new robot applications.
1.Differences from the conventional robot hand model
previous version | new version | |
Finger size and shape |
|
|
Finger only additional purchase/exchange |
|
|
Finger surface material |
|
|
Vision-based-tactile software information |
|
|
Customizability |
|
|
Price |
|
|
2.New product concept
Conventional vision-based tactile robot hands have been able to handle various workpieces (irregular shapes, multi-product, soft, uneven loads, brittle objects, etc.) with one type of finger, as shown in the video below.
However the process, object and handling requirements are infinitely different depending on the industry, business, and product. Conventional fingers have been criticized as being too large and too thick, which poses handling problems when implemented into production lines even when they can actually pick up the workpiece. By making it possible to select fingers from a variety of sizes and shapes, replace them, expand their functions, and customize them, FingerVision can respond to each customer's challenges and needs. You can select the vision-based tactile robot hand that best fits your needs.
3.Basic edition: 4 standard lineups
Cyl1 :curved gripping surface
The curved gripping surface enables handling of cylindrical workpieces, workpieces bundled (like brushes), and thin wafers.
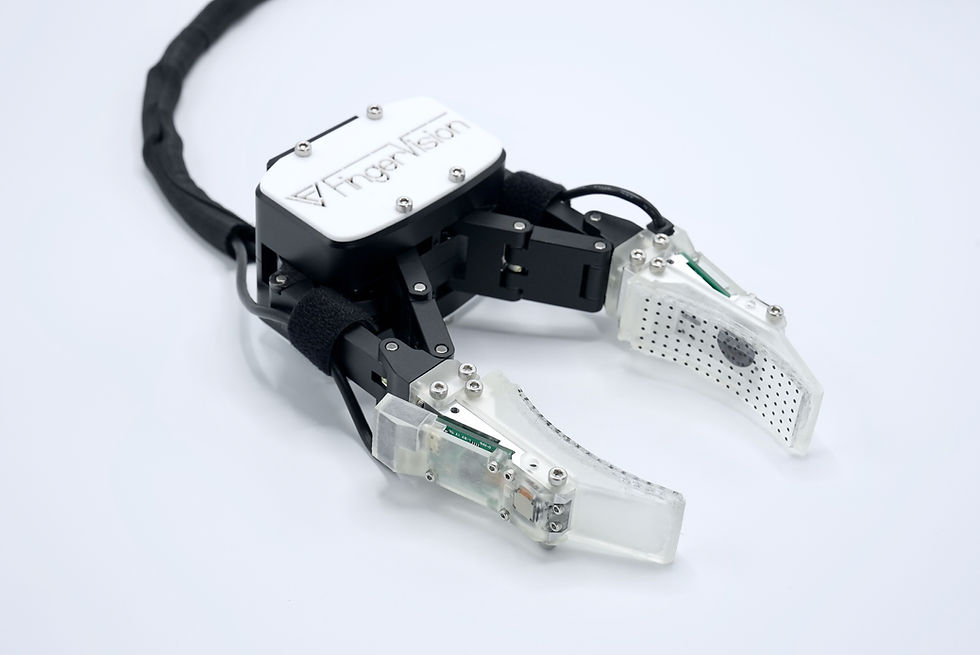
SS2 :shape is thinner than a human fingertip
The shape is thinner than a human fingertip, making it versatile when picking/placing in bulk or when space is narrow, or when handling small workpieces.

α on β :Highly versatile shape
With short distance from the gripper, gripping force can be transmitted without loss. This is an upgraded version of the previous shape and provides the same versatility as before.

M6 :Shape that wraps around fragile workpieces
It has the same shape as the fingers used in the food industry's "food plating robots*" (however, there is no removal mechanism). The cup-shaped handle creates friction by creating unevenness on the gripping surface, allowing naive handling with less gripping force for soft, irregularly shaped workpieces, such as foodstuffs.
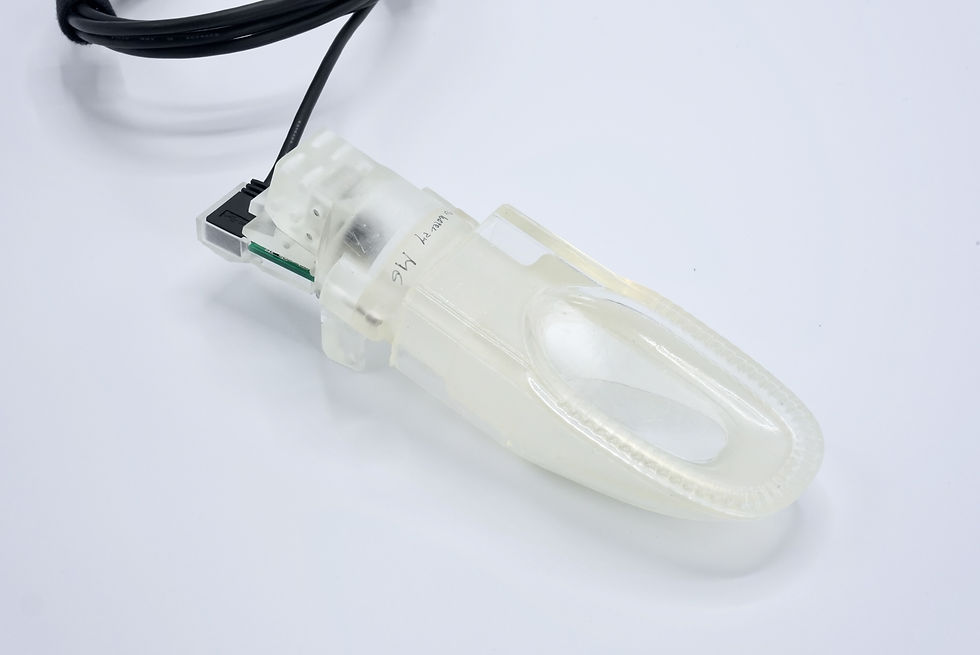
3.Further advanced edition: Specific examples of customization
L1 Palm size vs. previous size
The large palm-sized gripping surface allows more surfaces to come into contact with the workpiece, allowing handling with less gripping force. This allows for stable handling even with large workpieces or when there is little friction.
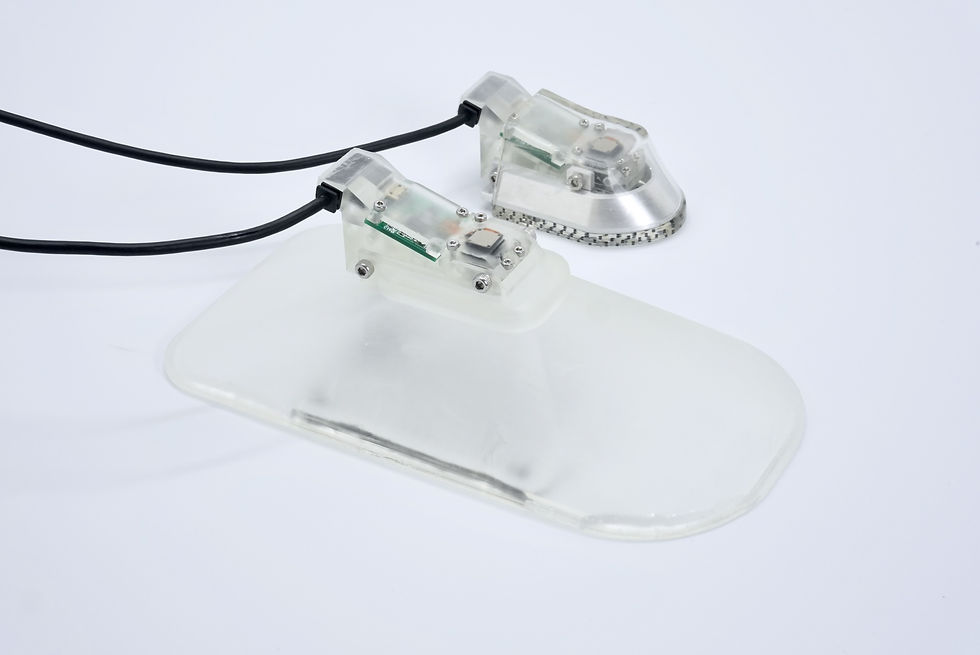